优化蒸汽供应系统
提高蒸汽压力和温度:在设备安全和工艺允许的范围内,适当提高进入硫化罐的蒸汽压力和温度,能增加蒸汽携带的热量,加快热量传递给被硫化物的速度,从而提升加热效率。
改进蒸汽管道设计:优化蒸汽管道的布局和直径,减少弯头、阻力件等,降低蒸汽在输送过程中的压力损失和热量散失。采用合适的保温材料对蒸汽管道进行良好保温,可有效减少热量向周围环境的散发,保证蒸汽到达硫化罐时仍具有较高的热量和压力。
安装蒸汽稳压装置:安装蒸汽稳压装置可以确保进入硫化罐的蒸汽压力稳定,避免因压力波动导致的加热不均匀和效率降低问题。
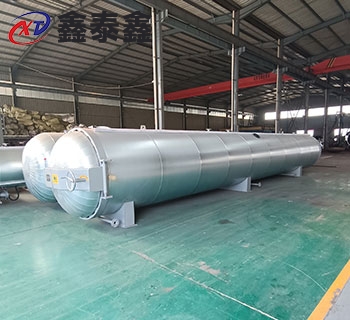
改善硫化罐的结构设计
增加加热面积:通过在硫化罐内部合理增加加热元件的数量或面积,如增加蒸汽散热管的长度、数量或采用翅片式散热管等,可增大蒸汽与硫化罐内空气或被硫化物的接触面积,使热量传递更加充分,提高加热效率。
优化罐体形状和内部布局:设计合理的罐体形状,如采用椭圆形或球形封头,可减少内部气流死角,使蒸汽在罐内流动更加顺畅,热量分布更均匀。合理布置被硫化物的放置位置和方式,避免局部堆积导致热量传递受阻,确保蒸汽能够充分接触到每个被硫化物。
提高罐体保温性能:选用导热系数低、保温性能好的材料对硫化罐进行保温处理,如采用陶瓷纤维、聚氨酯泡沫等高效保温材料,可有效减少热量从罐体内向外界的散失,提高热量利用率,进而提升加热效率。
强化热交换过程
采用高效热交换器:在硫化罐的蒸汽回路中安装高效热交换器,可使蒸汽与被加热介质(如空气、水等)之间进行更充分的热量交换,提高热能传递效率。
增强气流循环:安装循环风机等装置,加强硫化罐内的空气或蒸汽的循环流动,使热量能够更快速、均匀地传递到各个部位。合理设计循环风道,确保气流能够覆盖整个硫化罐空间,避免出现局部温度过高或过低的情况。
精确的控制系统
安装先进的温度传感器:在硫化罐内关键位置安装高精度、响应速度快的温度传感器,实时准确地监测罐内温度变化,为控制系统提供精确的温度数据。
采用智能控制系统:运用先进的智能控制算法,如 PID 控制、模糊控制等,根据温度传感器反馈的信息,自动精确调节蒸汽流量、循环风机转速等参数,使硫化罐内温度快速稳定地达到设定值,并保持在一个较小的波动范围内,提高加热效率和温度控制精度。
定期维护与保养
检查和清理加热元件:定期检查蒸汽散热管、加热板等加热元件,及时清理表面的污垢、水垢和铁锈等,以保证热量能够有效地从加热元件传递到被加热物体上。
维护蒸汽系统:对蒸汽锅炉、蒸汽管道、阀门等蒸汽系统设备进行定期维护,确保其正常运行,避免因设备故障导致的蒸汽供应不足或不稳定,影响加热效率。